Motor Starter vs Contactor: Which One Should I Use?
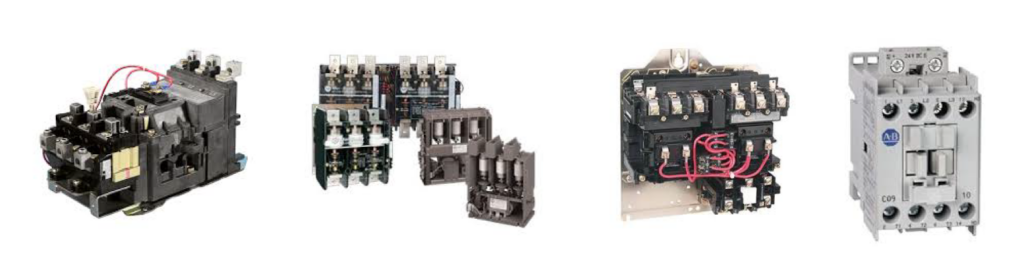
In industrial electrical systems, precision, reliability, and safety are paramount. Every component plays a vital role in ensuring the smooth operation of machinery and processes. These systems are designed to handle high power loads and ensure the safe and efficient distribution of electricity. The proper functioning of these systems relies heavily on the quality and compatibility of their components.
Two key elements that frequently come into play are motor starters and contactors. While these components may appear similar, they serve distinct purposes, and selecting the right one for your specific application can significantly impact system performance and safety.
A contactor is an electrically controlled switch used for switching power circuits. It is typically employed to control electric motors, lighting, heating, and other electrical loads. A motor starter goes a step further than a contactor. While it includes a contactor as a key component, it also incorporates overload protection and, in many cases, control circuitry. Motor starters are specifically designed to safely start and stop electric motors.
Top brands like Allen-Bradley, Siemens, Schneider Electric, Eaton, and GE offer a variety of motor starters tailored to different motor sizes and applications.
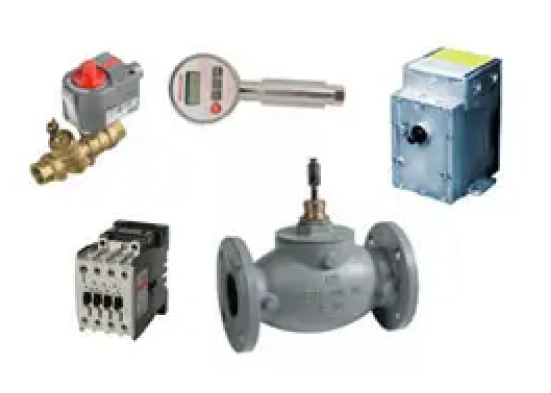
Shop Our Automation Control Equipment & Products
How Do Contactors Work?
A contactor’s primary role is to control the on/off operation of electrical equipment such as motors, heaters, lighting, and pumps in industrial settings. Unlike manual switches, contactors are remotely operated, making them ideal for automated systems.
- Core Components: A contactor consists of an electromagnet (coil), contacts, and an enclosure.
- Operating Mechanism: When the coil is energized, it creates a magnetic field that pulls the contacts together, completing the circuit. De-energizing the coil opens the contacts, interrupting the circuit.
- Control Circuit: The coil is activated by a low-power control circuit, allowing the safe switching of high-power loads.
Common Applications of Contactors
Contactors are widely used for on/off control in:
- Electric Motors: For example, starting and stopping conveyor belts in manufacturing plants.
- Lighting Systems: Automated control of large-scale lighting, such as in stadiums or warehouses.
- Heaters and HVAC Systems: Switching heating elements or air conditioning units.
- Pumps: Controlling water pumps in industrial processes.
Examples from Leading Brands
- Allen-Bradley (Rockwell): Offers durable contactors like the Bulletin 100-C series, ideal for high-demand motor control.
- Siemens: Known for their SIRIUS line, featuring compact designs for space-saving applications.
- Eaton (Cutler-Hammer): Provides versatile contactors with built-in surge suppression for HVAC and motor systems.
- Schneider Electric: Their TeSys D contactors are widely used for both AC and DC applications, offering reliability and ease of maintenance.
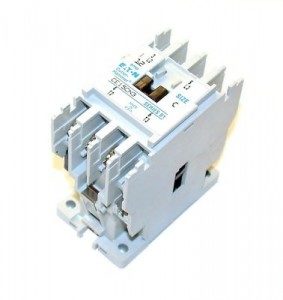
Shop Our Industrial HVAC Contactors and Relays
How Does a Motor Starter Work?
Motor Starters incorporate key functionalities that go beyond the basic switching role of contactors, most notably built-in overload protection, which safeguards motors against damage caused by excessive current or overheating.
Key Features of Motor Starters
- Motor Control: Enables safe starting and stopping of motors, often incorporating soft-start features to reduce wear and tear on mechanical systems.
- Overload Protection: Built-in protection devices monitor current levels and disconnect the motor if it exceeds safe operating limits.
- Integrated Design: Combines a contactor, overload relay, and sometimes additional control circuitry in one unit.
How Overload Protection Works
- Overload protection is typically implemented using thermal relays or electronic overload relays. Thermal Overload Relays use a bimetallic strip that bends when heated by excess current, triggering a disconnect. Electronic Overload Relays offer precise current monitoring and can include advanced features like phase-loss detection and adjustable trip settings.
- This protection ensures that motors are shielded from conditions like excessive load, phase imbalance, or overheating.
Examples of Motor Starter Series from Leading Brands
Allen-Bradley (Rockwell Automation): The 100-E and 193-EE series integrate contactors and overload relays, offering flexibility and modularity. Designed for medium and large motors in demanding applications.
Siemens: The SIRIUS 3RW series soft starters provide gradual motor ramp-up and overload protection, ideal for conveyor systems and pumps.
Schneider Electric: The TeSys GV series includes manual motor starters with magnetic and thermal protection, compact for space-constrained installations.
Eaton (Cutler-Hammer): The XTCE series combines rugged contactors with thermal and electronic overload relays, tailored for industrial environments.
GE (General Electric): The CR306 series motor starters offer thermal overload protection and are built for heavy-duty applications.
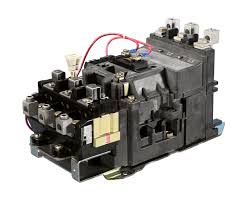
Shop Our Industrial Motor Starters
What is The Major Differences Between a Contactor and a Motor Starter
Feature | Contactors | Motor Starters |
---|---|---|
Primary Function | Used for remote switching of power circuits, controlling the flow of electricity to equipment. | Designed specifically for controlling and protecting motors, including starting, stopping, and overload protection. |
Overload Protection | No built-in overload protection; requires external devices for monitoring and protection. | Includes integrated overload protection (thermal or electronic) to safeguard motors from damage caused by overheating or excessive current. |
Design and Components | Simpler design with three key parts: an electromagnet (coil), fixed and movable contacts, and an enclosure. | More complex design combining a contactor, overload relay, and sometimes advanced control circuitry. |
Usage | General-purpose on/off control for various electrical loads, including lighting, heating, and small motors. | Dedicated to motor control, ensuring smooth operation and protection under different load conditions. |
Typical Applications | – Lighting systems (e.g., warehouses, stadiums). – Heating elements and HVAC systems. – Industrial equipment requiring frequent switching. | – Industrial motors used in conveyor belts, pumps, compressors, and fans. – High-load systems requiring overload protection. – Applications where motor damage due to overcurrent must be avoided. |
Control Options | Operated by a low-power control circuit, enabling remote on/off control but lacking advanced features. | Offers more advanced control options, including adjustable overload trip settings and sometimes soft-start features to reduce stress on motors. |
Complexity | Simpler device; focuses solely on switching operations. | Multifunctional device; manages motor operation and protects against faults, offering greater system reliability. |
Cost | Generally lower cost due to simpler functionality and fewer components. | Higher cost due to added functionality, protection features, and integrated components. |
Maintenance | Requires external protective devices for full functionality, increasing potential maintenance effort. | Integrated protection reduces the need for additional components, simplifying maintenance. |
Fault Handling | No capability to detect or handle overloads or faults. Relies on external devices for such monitoring. | Automatically disconnects the motor during overload or fault conditions, minimizing equipment damage and downtime. |
Selecting the Right Component for Your Application
Step 1: Evaluate Your Application Needs
Is your goal simply to control on/off switching, or do you also need motor-specific control and protection? Use a contactor for general-purpose switching (e.g., lighting, heaters). Use a motor starter if you need to protect motors from overload or fault conditions. For high-power loads like motors, consider motor starters.
Step 2: Understand Electrical Specifications
Match the component’s specifications to your application. Ensure the device can handle the voltage and current of your load. For large motors, choose a motor starter with appropriate thermal or electronic overload protection. Verify compatibility with single-phase or three-phase systems. If there will be frequent switching, choose a durable contactor designed for high-duty cycles. For infrequent operation, a simpler device would be sufficient.
Step 3: Consider Environmental Factors
If the device will be exposed to extreme temperatures, dust, vibration, or moisture, choose components with NEMA or IP ratings for harsh conditions. For limited space, look for compact designs, such as motor starters that integrate contactors and overload relays. If overload or fault handling is critical, a motor starter with built-in thermal or electronic overload protection is essential.
Step 4: Consult Experts or Manufacturer Specifications
When in doubt, consult documentation or manufacturers like Allen-Bradley, Siemens, Eaton, GE, or Schneider Electric for recommendations tailored to your application.
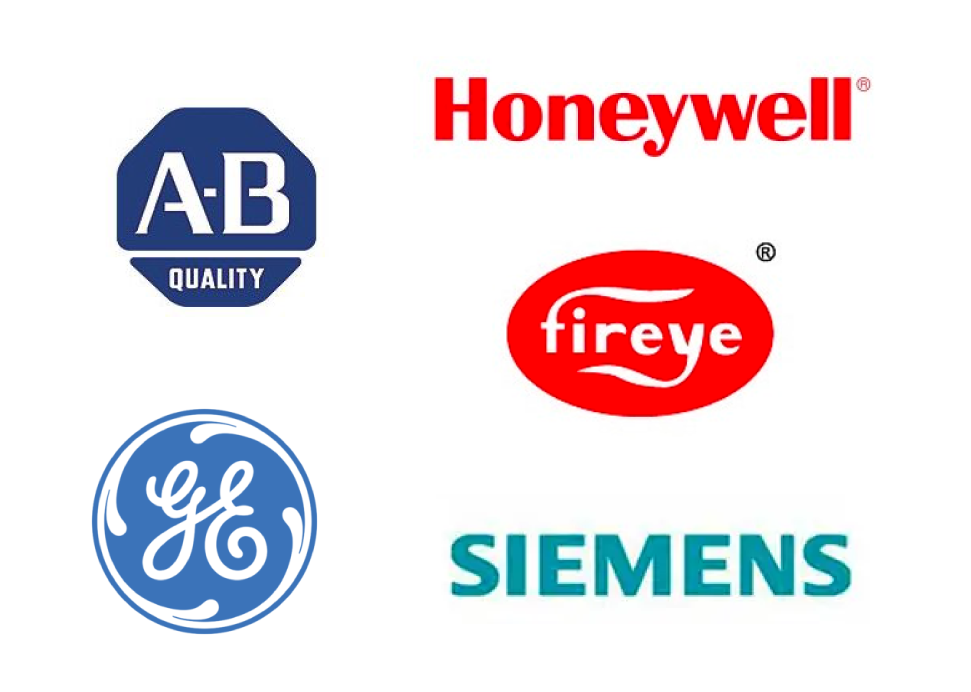
Shop From Our Industrial Control Manufacturers and Suppliers
Motor Starter vs Contactor – Frequently Asked Questions
- What are the primary uses of contactors in industrial systems?
Contactors are primarily used for remote on/off control of power circuits in systems such as lighting, heating, HVAC, and small motors. They are ideal for applications requiring frequent switching and high current loads. - How does overload protection in motor starters safeguard equipment?
Overload protection in motor starters monitors current levels and disconnects the motor when excessive current or overheating occurs, preventing equipment damage, downtime, and potential safety hazards. - When should a motor starter be chosen over a contactor?
Choose a motor starter when you need motor-specific control and protection, such as overload and fault handling, especially in applications like conveyor belts, pumps, and compressors. - What environmental factors should be considered when selecting these components?
Consider ambient temperature, exposure to dust, moisture, or chemicals, and the need for protective enclosures like NEMA or IP-rated housings for harsh industrial environments. - How do cost and complexity differ between contactors and motor starters?
Contactors are less expensive and simpler, focusing on switching. Motor starters are costlier but offer integrated overload protection and advanced control features, reducing the need for additional devices.