A Guide To Different Types of Furnace Burners & Selection
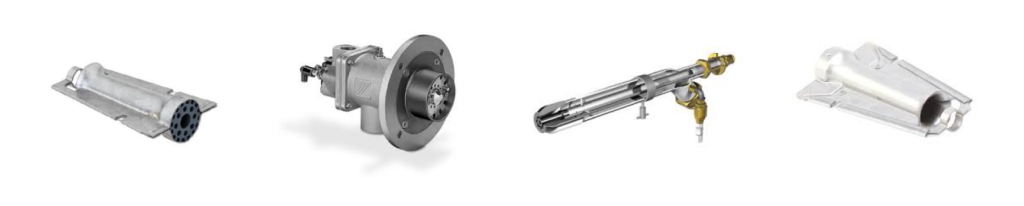
Overview of Furnace Burners
Furnace burners are critical components of furnace boilers. They facilitate the combustion process by mixing fuel (e.g., natural gas, oil, coal) with air in the right proportions and igniting it to produce a controlled flame. Top manufacturers include Honeywell, Cleaver Brooks, Fives North American, and Power Flame
Roles and Functionalities of Burners:
- Fuel Combustion: Burners ensure efficient combustion of fuel to generate heat.
- Heat Control: Burners regulate heat output by controlling the fuel-air mixture and combustion process.
- Safety: Equipped with safety mechanisms, they prevent fuel leaks or incomplete combustion.
- Efficiency: Modern burners optimize fuel consumption to minimize waste and emissions.
- Adaptability: Burners can handle various fuels, including natural gas, oil, or dual-fuel systems.
Furnace burners come in various types to suit different industrial needs. Forced draft burners use fans to push air into the burner, enhancing combustion efficiency and providing precise control. Atmospheric burners, on the other hand, rely on natural air drafts for combustion, making them simpler and more cost-effective for certain applications. For operations requiring environmental compliance, low-NOx burners are designed to minimize nitrogen oxide emissions. Additionally, dual-fuel burners offer versatility by being capable of operating on two different fuel types, such as natural gas and oil, making them adaptable to varying fuel availability and operational requirements.
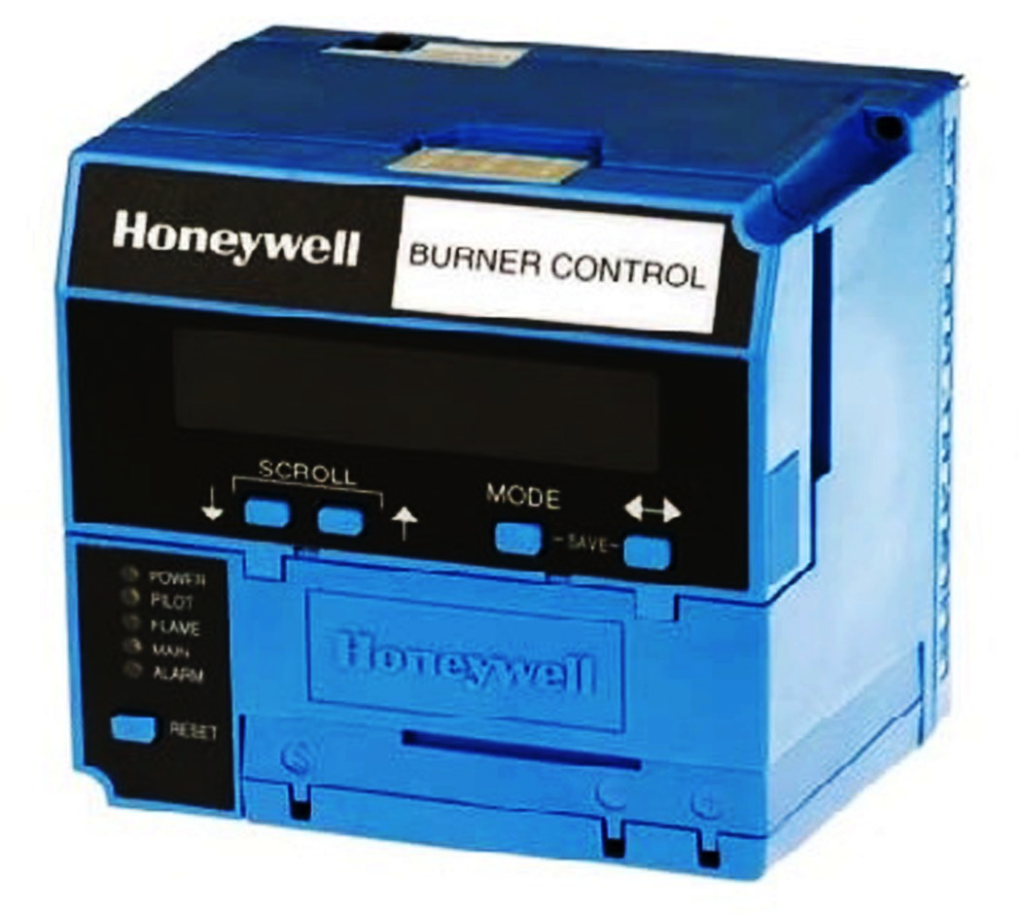
Shop Our Industrial and Commercial Burner Controls
Types of Furnace Burners
Natural Gas Burners
Natural gas burners are designed for clean combustion, using natural gas as a fuel source to minimize pollutants. Their construction includes features for precise air-to-fuel mixing and adaptability to various heating requirements. The use of natural gas burners reduces environmental impact through lower emissions of CO₂ and nitrogen oxides (NOx). They are cost-effective due to high fuel efficiency and reduced maintenance needs, and they provide consistent heat output, ensuring reliability in industrial processes. Natural gas burners work by mixing natural gas and air in controlled proportions. The mixture is ignited to generate heat, which can be directed to the required industrial application. Advanced models include monitoring systems to optimize combustion and improve safety. Industries utilize natural gas burners in a wide range of processes. They are integral to boiler systems for generating steam, metal treatment for forging and annealing, drying systems in food and textiles, and chemical plants for heating and refining. These versatile applications make natural gas burners a cornerstone of industrial heating solutions.
Aspect | Details |
---|---|
Characteristics | – Designed for clean and efficient combustion. – Equipped with advanced controls for precise air-to-fuel ratio. – Can handle varying heat demands. |
Benefits | – High energy efficiency. – Lower greenhouse gas and NOx emissions. – Reduced operating costs. – Reliable and consistent heat output. |
Operational Mechanisms | – Mixes natural gas with air in a controlled ratio. – Ignites the mixture to produce heat. – Advanced designs include flame monitoring and safety features. |
Applications | – Used in boilers for steam generation. – Heat treatment in metal industries. – Drying processes in food and textiles. – Chemical processing and refining. |

Shop Our Industrial and Commercial Flame Safety Devices
Oil Burners
Oil burners are key components in industrial heating systems that use liquid fuels, such as diesel, kerosene, or heavy oils, to generate heat. They are known for their robust performance and flexibility in handling a variety of fuel types. Oil burners are often used in settings where natural gas is unavailable or impractical. Oil burners are versatile and can handle a range of liquid fuels, from light oils like diesel to heavier fuels requiring preheating. They are built to withstand harsh industrial conditions and deliver consistent performance in high-temperature environments. The flexibility of oil burners to operate with various fuel types makes them a practical choice for industries in remote locations. They produce high heat output, making them suitable for energy-intensive applications, and their durable design ensures long operational life, reducing maintenance costs. Oil burners typically preheat heavier fuels to achieve the optimal viscosity for combustion. The fuel is atomized into fine droplets and mixed with air, then ignited to produce a stable flame. Advanced designs include safety features such as flame monitoring and automatic shutdown in case of malfunction.
Oil burners are widely used in industrial boilers for steam and hot water generation, as well as in furnaces for processes like forging and annealing in the metal industry. They are also employed in drying systems for agriculture and construction, asphalt production, and chemical manufacturing processes, offering flexibility and efficiency for various industrial heating needs.
Aspect | Details |
---|---|
Characteristics | – Capable of burning a wide range of liquid fuels. – Durable design for high-temperature environments. – Include preheating for heavy oils. |
Benefits | – Versatile fuel options. – High heat output for demanding industrial processes. – Reliable operation in remote locations. – Long lifespan. |
Operational Mechanisms | – Preheats heavy oils for optimal viscosity. – Mixes atomized fuel with air for combustion. – Equipped with flame monitoring for safety. |
Applications | – Boilers for steam and hot water generation. – Industrial furnaces for metal processing. – Drying systems in agriculture and construction. – Asphalt plants and chemical manufacturing. |
Dual-Fuel Burners
Dual-fuel burners are versatile heating components designed to operate on two different types of fuels, typically natural gas and oil. They provide flexibility and reliability in industrial heating systems, ensuring uninterrupted operations even when one fuel source is unavailable. These burners are widely used in industries requiring adaptable and efficient heating solutions. Dual-fuel burners are engineered to burn both gaseous and liquid fuels, such as natural gas and oil. They feature automatic fuel-switching mechanisms that enable seamless transitions between fuels. These burners are optimized for efficiency and include controls to minimize emissions. The ability to operate on multiple fuels offers unparalleled flexibility, ensuring that industries can continue operations even during fuel supply disruptions. Dual-fuel burners enable cost savings by allowing the use of the most economical or readily available fuel. When operating on natural gas, they produce lower emissions, supporting environmental compliance and sustainability goals. Dual-fuel burners have separate fuel supply lines for gas and oil, and the burner automatically adjusts the air-to-fuel ratio depending on the fuel in use. Advanced designs can switch between fuels without interrupting the heating process, ensuring reliability and operational continuity.
These burners are widely utilized in industrial boilers for steam and hot water production. They are also employed in kilns and furnaces for metalworking and ceramics, drying systems in food and textile industries, and power generation plants. Their adaptability makes them an ideal choice for industries requiring dependable and efficient heating solutions.
Aspect | Details |
---|---|
Characteristics | – Capable of operating on both natural gas and oil. – Equipped with automatic fuel-switching capabilities. – Designed for high efficiency and low emissions. |
Benefits | – Fuel flexibility ensures continuous operation. – Reduces dependency on a single fuel source. – Cost optimization by using the most economical fuel. – Lower emissions when using natural gas. |
Operational Mechanisms | – Includes separate fuel supply lines for gas and oil. – Automatically adjusts air-to-fuel ratio for each fuel. – Can switch between fuels without interrupting operations. |
Applications | – Industrial boilers for steam and hot water. – Kilns and furnaces in the metal and ceramic industries. – Food processing and drying systems. – Power generation and chemical manufacturing. |
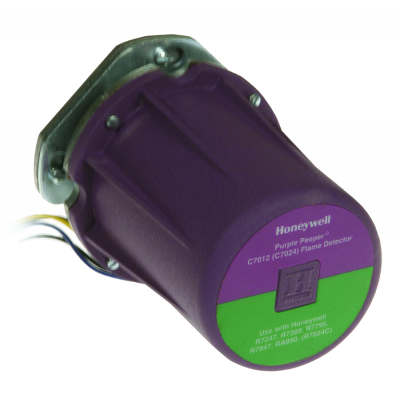
Shop Our Industrial Flame Sensors and Scanners
Low-NOx Burners
Low-NOx burners are specialized heating devices designed to minimize the emission of nitrogen oxides (NOx), which are harmful pollutants contributing to smog and acid rain. These burners are essential for industries operating under strict environmental regulations, providing both efficiency and cleaner combustion. They are specifically designed to reduce nitrogen oxide emissions during combustion. They achieve this through advanced combustion techniques like staged combustion, where fuel is introduced in stages, and flue gas recirculation, which cools the flame and lowers NOx formation.
These burners significantly reduce harmful NOx emissions, helping industries meet environmental standards and avoid penalties. They also improve overall combustion efficiency, leading to cost savings on fuel. Their optimized design often results in longer equipment life and reduced maintenance requirements. In order to reduce emissions, staged combustion introduces fuel in phases to reduce flame temperature, while flue gas recirculation recycles part of the exhaust gases back into the burner to cool the flame.
Low-NOx burners are widely used in industrial boilers and power generation plants to produce steam and electricity. They are also employed in metalworking furnaces for heat treatment, chemical plants for processing and refining, and food and textile industries for drying systems. Their environmentally friendly design makes them a preferred choice in regions with strict air quality regulations.
Aspect | Details |
---|---|
Characteristics | – Engineered for reduced NOx emissions. – Advanced combustion technology for clean burning. – Incorporates flame stabilization and precise fuel-air mixing. |
Benefits | – Reduces environmental impact. – Helps industries comply with emissions regulations. – Improves combustion efficiency. – Lowers operational costs through optimized fuel use. |
Operational Mechanisms | – Utilizes staged combustion or flue gas recirculation (FGR). – Precise control of air and fuel ratios. – Enhances flame stability for cleaner burning. |
Applications | – Power generation and industrial boilers. – Metalworking furnaces and heat treatment processes. – Chemical plants and refineries. – Food processing and drying systems. |
Selecting the Right Furnace Burner
Fuel Availability and Its Influence on Burner Selection
- Regional Fuel Access: Local availability of natural gas, oil, or alternative fuels directly affects burner choice to ensure consistent supply and operational reliability.
- Cost Efficiency: The cost of fuels in a given area can drive selection, favoring burners compatible with the most economical fuel.
- Fuel Storage Requirements: Burners using liquid fuels (e.g., oil) may require on-site storage, influencing preferences in space-limited or regulatory-heavy regions.
- Flexibility Needs: Dual-fuel burners are chosen in areas with variable fuel availability, allowing seamless switching between gas and oil.
- Environmental Regulations: Regions with strict emissions laws may prioritize burners optimized for cleaner fuels like natural gas or low-NOx designs.
- Supply Chain Stability: Industries in remote or volatile areas may prefer burners that can handle multiple fuels to mitigate supply interruptions.
Process Temperature Requirements
In order to match burners with the required industrial temperatures:
- Process Efficiency: Ensuring the burner can achieve the required temperature optimizes energy usage and enhances the overall efficiency of the industrial process.
- Material Integrity: Precise temperature control prevents damage to materials being processed, such as warping in metals or uneven curing in ceramics.
- Product Quality: Consistent and accurate temperatures are essential for maintaining uniformity and high-quality output in processes like food production or chemical reactions.
- Energy Optimization: Burners matched to the required temperature range avoid energy waste and reduce operational costs by preventing over- or under-heating.
- Safety: Using burners capable of maintaining the necessary temperatures reduces risks of overheating, equipment failure, or accidents in the industrial environment.
- Compliance: Specific industrial processes often require adherence to regulated temperature ranges to meet standards and certifications.
- Burner Longevity: Properly matching the burner to the process prevents undue stress on the equipment, prolonging its lifespan and minimizing maintenance needs.
Environmental Regulations
Environmental regulations play a significant role in burner selection by prioritizing technologies that minimize emissions and meet compliance standards. Industries in regions with strict air quality laws often choose low-NOx or ultra-low-NOx burners to reduce nitrogen oxide emissions. Burners using cleaner fuels like natural gas are favored for their lower greenhouse gas output. Regulations also drive demand for advanced burners with efficient combustion and monitoring systems to limit pollutants. Compliance not only avoids penalties but also supports sustainability goals, making environmentally friendly burners a strategic and operational necessity.

Shop Our UV Flame Detectors and Sensors
Maintenance Needs and System Compatibility
Effective maintenance practices and compatibility with control systems are critical for ensuring optimal burner performance and longevity. Routine maintenance tasks, such as cleaning fuel lines, inspecting flame sensors, and calibrating air-to-fuel ratios, help prevent inefficiencies and reduce downtime. The compatibility of burners with existing control systems is essential for seamless operation; modern burners often require advanced controls capable of precise combustion management and emissions monitoring. Retrofitting burners to older systems may involve upgrading control components to ensure proper functionality. Dual-fuel or low-NOx burners, for example, often need specific controllers to manage fuel switching or maintain low emissions. Regular system integration checks and collaboration with manufacturers help align burners and controls, maximizing efficiency, safety, and compliance with industrial standards.
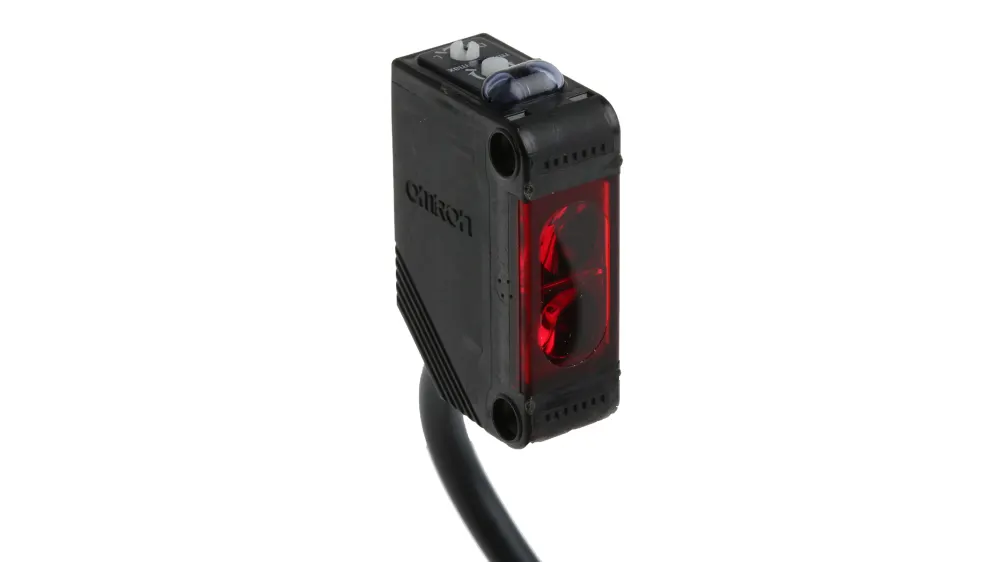
Shop Our Industrial and Commercial Sensors
Types of Furnace Burners – Frequently Asked Questions
- What are the key differences between types of gas furnace burners and propane burners?
- Propane burners are designed for higher combustion energy and require smaller orifices, while natural gas burners handle lower energy density fuels with larger orifices.
- How do I calculate the energy efficiency of different types of furnace burners?
- Measure the input fuel energy (BTUs) and the output heat energy delivered to the process. Efficiency (%) = (Output Energy ÷ Input Energy) × 100.
- What are the safety considerations when choosing a furnace burner?
- Evaluate flame stability, fuel leakage prevention, proper combustion monitoring, and adherence to safety codes and standards.
- How often should different types of burners be maintained?
- Light-duty burners (e.g., residential): annually; heavy-duty industrial burners: quarterly to bi-annually based on usage and fuel type.
- What are the initial steps to retrofitting an older furnace with a new burner type?
- Assess compatibility, upgrade controls if needed, evaluate venting and fuel supply, and consult manufacturers for system recommendations.