How to Make a Thermocouple: A Guide with Pyromation Parts
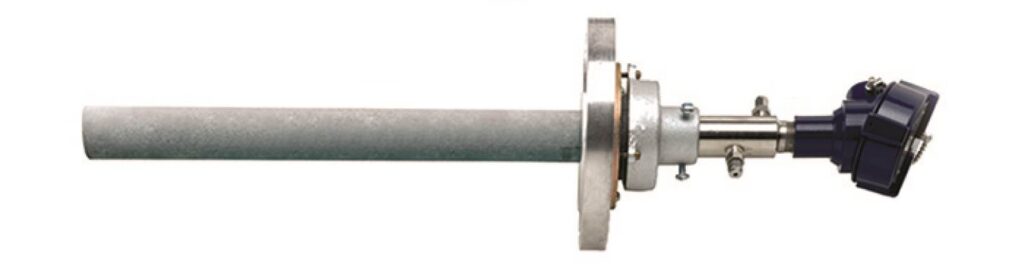
In this guide we will learn how to build a thermcouple, what they are, and how to use them. Thermocouples are temperature measurement devices that operate based on the Seebeck effect, which states that when two dissimilar metals are joined at one end and exposed to temperature variations, a voltage is generated proportional to the temperature difference. This voltage is then interpreted by a measurement system to determine the temperature. Thermocouples are widely used in industrial applications due to their durability, wide temperature range capabilities, and fast response times. They are commonly found in manufacturing, metal processing, energy production, and chemical industries, where accurate and reliable temperature monitoring is essential for process control, safety, and efficiency.
Thermocouples are widely used in industrial and scientific applications because they are durable, fast-responding, and capable of measuring a wide range of temperatures. They come in different types, including Type K, J, T, and N, each suited for specific environments and temperature ranges.
Pyromation is a well-respected manufacturer of thermocouples, producing high-quality sensors designed for various industrial environments. Their product line includes thermocouples with a variety of sheath materials, calibration types, and protective coatings to withstand harsh conditions, including high temperatures, corrosive atmospheres, and heavy vibrations. Pyromation thermocouples are often used in applications such as furnace temperature monitoring, food processing, power generation, and petrochemical processing. Additionally, Pyromation offers custom-engineered solutions tailored to specific industrial needs, ensuring compatibility with existing systems and optimal performance. Their thermocouples are typically accompanied by thermowells, connection heads, and transmitters to enhance durability and signal transmission.
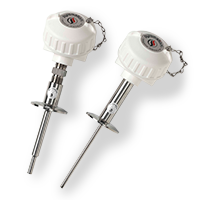
Shop Our Industrial and Commercial Thermocouples
Questions to Ask when Building a Thermocouple
- What type of Thermocouple? (i.e. Type J, Type K)
- What is the length of the sheath?
- What is the OD (outer diameter) of the sheath?
- ¼” is standard
- if ¼” or smaller is needed, proceed to #4
- If you need something larger, skip to #9
- What type of sheath?
- Stainless steel or inconel? (inconel is for higher temps – over 1000 degrees)
- Do you need a fitting underneath the head?
- If yes, what size?
- Cold Termination:
- Do you need a screw cover head?
- Cast iron
- Explosion proof (stainless steel)
- Polypropolene (used in the food industry)
- Or do you need a plug or jack?
- If yes, do you need a mating jack with your plug?
- Do you need a screw cover head?
- Spring Wire Transition: Instead of a head, some thermocouples have a spring wire transition
- What is the length?
- What is the outer workings of the wire?
- PVC
- Teflon
- Fiberglass (for higher temps)
- Stainless steel overbraid
- Armor cable
- Is it a Duplex?
- Normal thermocouples have 2 wires, a duplex thermocouple gets double readings (4 wires)
- Normal RTDs have 3 wires, a duplex RTD gets double readings (6 wires)
- If the OD is larger than ¼”:
- What material? Ceramic or iconel?
- Do you want a fitting? These usually come with heads
- Length and OD
- Can you send a picture?
Thermocouples Types and Temperature Ranges
1. Type K (Nickel-Chromium / Nickel-Alumel)
Range: −200°C to +1,260°C (−328°F to +2,300°F)
Most common type – inexpensive, wide range.
Use: General purpose; used in ovens, engines, kilns.
Notes: Good oxidation resistance, but not ideal in vacuum or reducing atmospheres.
2. Type J (Iron / Constantan)
Range: −40°C to +760°C (−40°F to +1,400°F)
Use: Older equipment, internal combustion engines.
Notes: Iron wire is prone to rusting, so not ideal in moist environments. Best in vacuum or inert atmospheres.
3. Type T (Copper / Constantan)
Range: −200°C to +370°C (−328°F to +700°F)
Use: Low-temperature applications like cryogenics and labs.
Notes: Very stable and accurate at low temps; limited upper range.
4. Type E (Chromel / Constantan)
Range: −200°C to +870°C (−328°F to +1,598°F)
Use: Environments requiring high accuracy and stability.
Notes: Higher output (mV) than Type K or J, good in oxidizing atmospheres.
5. Type N (Nicrosil / Nisil)
Range: −200°C to +1,300°C (−328°F to +2,372°F)
Use: High-temperature, long-term stability required (aviation, power plants).
Notes: More stable than Type K at high temps; resistant to drift and oxidation.
6. Type S (Platinum-Rhodium 10% / Platinum)
Range: 0°C to +1,480°C (32°F to +2,696°F)
Use: Labs, metallurgy, glass industry.
Notes: Extremely stable and accurate; very expensive. Used as a reference standard.
7. Type R (Platinum-Rhodium 13% / Platinum)
Range: 0°C to +1,480°C (32°F to +2,696°F)
Use: Similar to Type S, but slightly higher Rhodium.
Notes: Very stable and also expensive.
8. Type B (Platinum-Rhodium 30% / Platinum-Rhodium 6%)
Range: +100°C to +1,700°C (212°F to +3,092°F)
Use: High-temp industrial processes, such as steel and glass manufacturing.
Notes: Most stable at extreme temperatures.
Summary Table:
Type | Temp Range (°C) | Metal Pair | Best For |
---|---|---|---|
K | -200 to +1260 | Chromel/Alumel | General purpose |
J | -40 to +760 | Iron/Constantan | Older systems |
T | -200 to +370 | Copper/Constantan | Cryogenic/low-temp |
E | -200 to +870 | Chromel/Constantan | High sensitivity |
N | -200 to +1300 | Nicrosil/Nisil | Stability/high-temp |
S | 0 to +1480 | Pt-Rh 10% / Pt | Lab/high-accuracy |
R | 0 to +1480 | Pt-Rh 13% / Pt | High-end industrial |
B | +100 to +1700 | Pt-Rh 30% / Pt-Rh 6% | Very high temp |
Understanding Thermocouple Components
Thermocouple Wire – Made of two dissimilar metals, selected based on temperature range and environmental conditions (e.g., Type K, J, T, N).
Junctions – The point where the two wires meet; can be grounded, ungrounded, or exposed, affecting response time and durability.
Insulation – Protects the wires from environmental damage; common types include fiberglass (high-temp), ceramic (extreme heat), and Teflon (chemical resistance).
Sheath Material – Stainless steel or ceramic tubing used to shield the thermocouple in harsh environments, improving longevity and performance.
Termination Components – Includes connection heads, terminal blocks, and transmitters, ensuring proper integration with monitoring systems.
- Thermowells – Protective casings that shield thermocouples from extreme conditions such as high pressure, corrosive environments, and mechanical damage while allowing easy replacement without disrupting the process.
Types of Materials – Thermocouple components are made from different materials depending on the application:
- Stainless Steel (general industrial use, corrosion-resistant)
- Inconel (high-temperature, oxidation-resistant)
- Hastelloy (chemical-resistant, ideal for harsh environments)
- Ceramic (extremely high temperatures, non-metallic)
- Teflon (chemical-resistant insulation, lower-temperature applications)
- Fiberglass (high-heat insulation, durable)
- Copper (used in extension wires for certain thermocouple types)
Practical Tips for Thermocouple Installation
Proper Placement for Accurate Readings
- Position the thermocouple as close as possible to the heat source or process to get precise temperature readings.
- Avoid placing it near heat sinks, cold junctions, or airflow disturbances that could cause inaccurate readings.
- Ensure full contact with the surface or medium being measured—use thermal paste or a heat-conductive compound if necessary.
Use Appropriate Mounting Methods
- Secure the thermocouple using clamps, brackets, or compression fittings to prevent movement and vibration.
- If inserting into a pipe or vessel, use a Pyromation thermowell to protect against pressure, corrosion, and mechanical damage.
- For immersion applications, ensure the thermocouple is deep enough into the medium (at least 10 times the diameter of the sheath) for stable readings.
Avoid Electrical Interference (Noise Reduction)
- Keep thermocouple wires away from high-voltage cables, motors, and power sources to minimize electromagnetic interference.
- Use shielded cables and proper grounding techniques to reduce signal noise.
- If extending the thermocouple wires, use Pyromation-compatible extension wire of the same type to maintain accuracy.
Ensure Secure and Clean Connections
- Tighten all terminal block screws to prevent loose connections that could lead to erratic readings.
- Keep connection points clean and free of corrosion, as oxidized terminals can create resistance and introduce errors.
- Use proper cold junction compensation if necessary to account for environmental temperature variations at the connection point.
Choose the Right Insulation and Sheathing
- Match insulation type to the environment: Teflon for chemical resistance, fiberglass for high heat, and ceramic for extreme temperatures.
- If the application involves moisture, oil, or harsh chemicals, select a sealed and corrosion-resistant sheath such as Inconel or Hastelloy.
Regular Calibration and Maintenance
- Periodically verify accuracy by comparing readings to a known reference temperature.
- Inspect thermocouple wires for damage, wear, or corrosion, especially in high-temperature or corrosive environments.
- Replace old or degraded thermocouples as they can drift over time, leading to inaccurate readings.
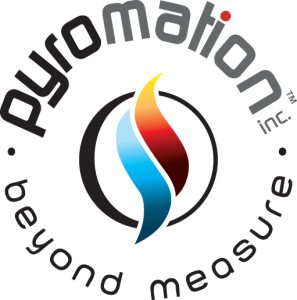
Shop our Pyromation Products
How to Make a Thermocouple – Frequently Asked Questions
How do I calibrate a thermocouple?
- Compare its readings to a known reference temperature (e.g., ice bath at 0°C or a precision-calibrated thermometer).
- Use a temperature calibrator or a dry-block calibrator for more precise industrial calibration.
- Adjust the connected measurement device or controller if needed.
What are the signs of a failing thermocouple?
- Inconsistent or erratic temperature readings.
- Slow response time or failure to reach expected temperatures.
- Visible wire damage, corrosion, or oxidation.
- Open circuit or no signal when tested with a multimeter.
How often should a thermocouple be replaced?
- Depends on usage conditions—typically every 6 months to 2 years in harsh environments.
- Replace if accuracy drifts beyond acceptable limits or physical damage is observed.
- Perform routine inspections and testing to determine if replacement is necessary.
Can a thermocouple be repaired, and how?
- Minor repairs: Reattach loose connections, clean terminals, or replace extension wires.
- Junction repair: Cut and re-weld the tip if the thermocouple junction is broken.
- Insulation fixes: Reinsulate exposed sections with high-temperature insulation if the protective layer is damaged.
- If severely damaged, replacement is recommended rather than repair.
What are the best practices for extending the life of a thermocouple?
- Use the correct sheath material (e.g., Inconel, stainless steel) for the application environment.
- Keep the thermocouple away from excessive vibration, moisture, and corrosive elements.
- Install it securely to prevent movement and strain.
- Regularly clean and inspect the thermocouple to prevent contamination or oxidation.
- Use thermowells in high-pressure or harsh environments for additional protection.